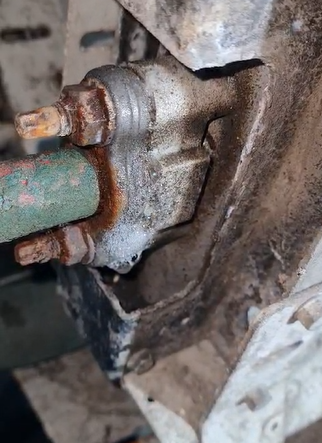
Client: Industrial Site in Heysham
Location: Heysham, UK
Date: October 2024
Equipment Type: Carrier Water Chiller with Aluminium-Copper Mechanical Joint
Issue: Corrosion and Refrigerant Leak Due to Joint Failure
Sustainability Index Score: 90%
Amount of Carbon Saved: 150.45 kg CO
Refrigerant Saved: 72 kg of R407C
Background
Lunar Refrigeration Ltd was called upon by the Site to resolve an issue with one of their Carrier Water Chiller units. The chiller uses a cast aluminium condenser coil connected to copper pipework via a mechanical joint. This configuration, while efficient, has shown a tendency for corrosion at the aluminium-copper joint, particularly where the factory-fitted seals are used.
Given the chiller’s critical role in supporting cooling processes at the station, the client required immediate intervention to prevent further refrigerant loss and performance reduction.
Problem Identification
Our inspection revealed significant corrosion and damage around the aluminium-copper joint, leading to a refrigerant leak. The factory-fitted seals, secured by two-holed flanges with nyloc nuts and washers, had deteriorated due to the effects of dissimilar metals and exposure to environmental factors over time.
Solution Implementation
To effectively repair the chiller and restore its functionality, Lunar Refrigeration Ltd carried out the following steps:
- Removal of Corroded Seals: The team removed the damaged factory-fitted seals and thoroughly cleaned the area to eliminate any residual corrosion.
- Replacement of Seals and Fasteners: New seals were fitted, and the joint was re-secured using two-holed flanges, nyloc nuts, and washers. This approach ensured a more robust and secure connection, mitigating the risk of future leaks.
- Testing: After reassembly, the chiller was pressurised and tested for leaks, confirming the integrity of the new seals and the stability of the connection.
Unfortunately, due to the limited imagery available, the repair process itself could not be documented in photos. The available images highlight the condition of the joint before the intervention, demonstrating the extent of the corrosion and leak.
Outcome
By replacing the corroded factory seals and re-securing the joint with flanges, nyloc nuts, and washers, Lunar Refrigeration Ltd successfully eliminated the leak and restored the chiller’s performance. This solution prevented the need for a costly condenser coil replacement and ensured that the chiller remained operational with minimal disruption to the Site’s processes.
Conclusion
This case study illustrates the importance of addressing joint failures promptly to prevent further damage to critical equipment. Lunar Refrigeration Ltd’s expertise in HVAC systems and experience with similar issues enabled us to implement a solution that restored equipment functionality efficiently. Our proactive approach minimised downtime and costs for the client while ensuring the long-term reliability of the chiller.